Product Quality
A holistic approach to ensuring consistency and quality
Our customers create products that make everyday life healthier, easier and safer: Food packaging that prolongs shelf life and prevents contamination. Drums that secure hazardous chemicals over thousands of miles and years of service. Caps that preserve the clean, crisp taste of water. That’s why we take a holistic approach to providing our customers with reliable, quality polyethylene.
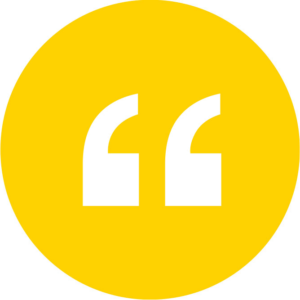
Quality is deeply embedded in our culture. Day in and day out, my goal is to enable NOVA Chemicals to consistently provide our customers with the exceptional polyethylene resins they have come to expect from us.”
Tony de Klerk
QUALITY PROJECT MANAGER
ISO 9001:2015
Our ISO 9001:2015 certification goes far beyond a document hanging on our facility walls. It’s proof of our promise to drive continuous improvement that enhances efficiency, eliminates waste and improves the customer experience.
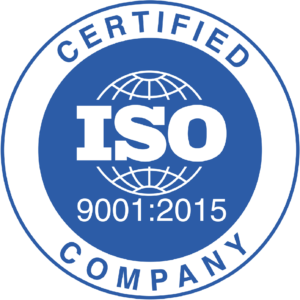
Advanced quality systems for our customers’ success
A 10-minute quality excursion at one of our plants can lead to a full day of production challenges for our customers. Our advanced testing and production systems help prevent these excursions from ever reaching our customers, so they can continue to produce top quality products with no unnecessary downtime or rework.
At-Line Testing
Consistent, defect-free polyethylene helps enable efficient, cost-effective production for our customers. To help us deliver the quality resins our customers count on, we have implemented at-line continuous polymer analysis technology at several of our plants. We use the data we gather from these systems to validate our product consistency and quality.
The at-line system continuously samples and tests our resin as it is being produced. Resin samples are obtained from the production stream and distributed to analytical equipment that measures product quality parameters including gels, black specks, additives, color, melt flow, pellet shape and size and pellet count.
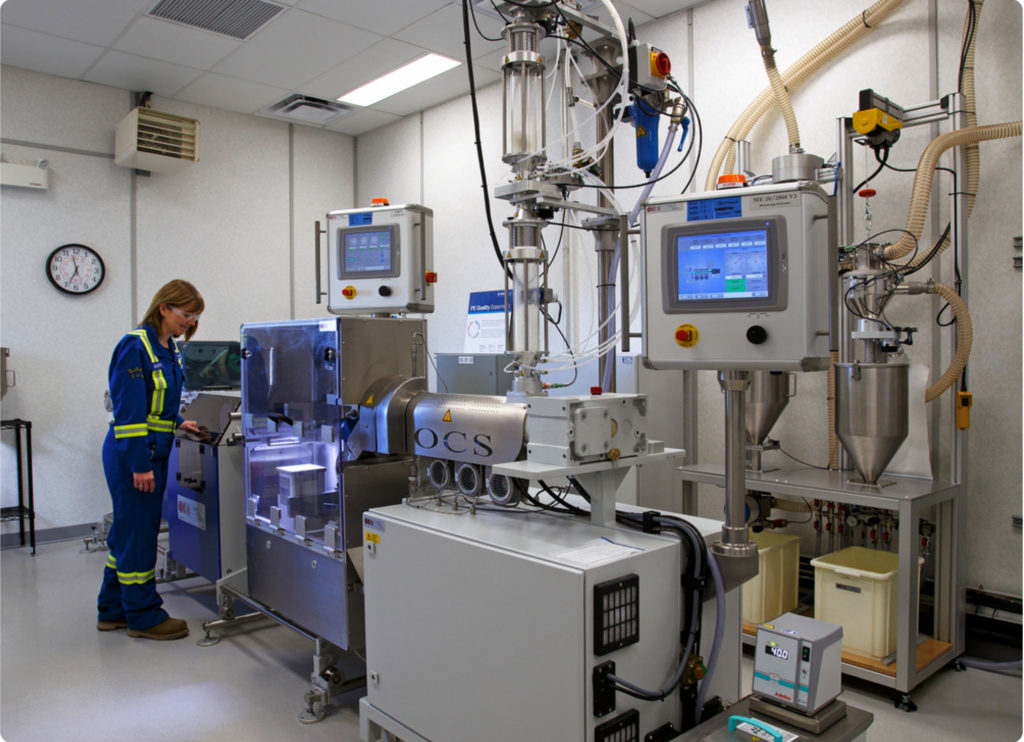
Process Control & Improvement
At-line high-frequency testing enables our operations teams to detect quality excursions, take corrective actions, and adjust operating conditions to help prevent future occurrences.
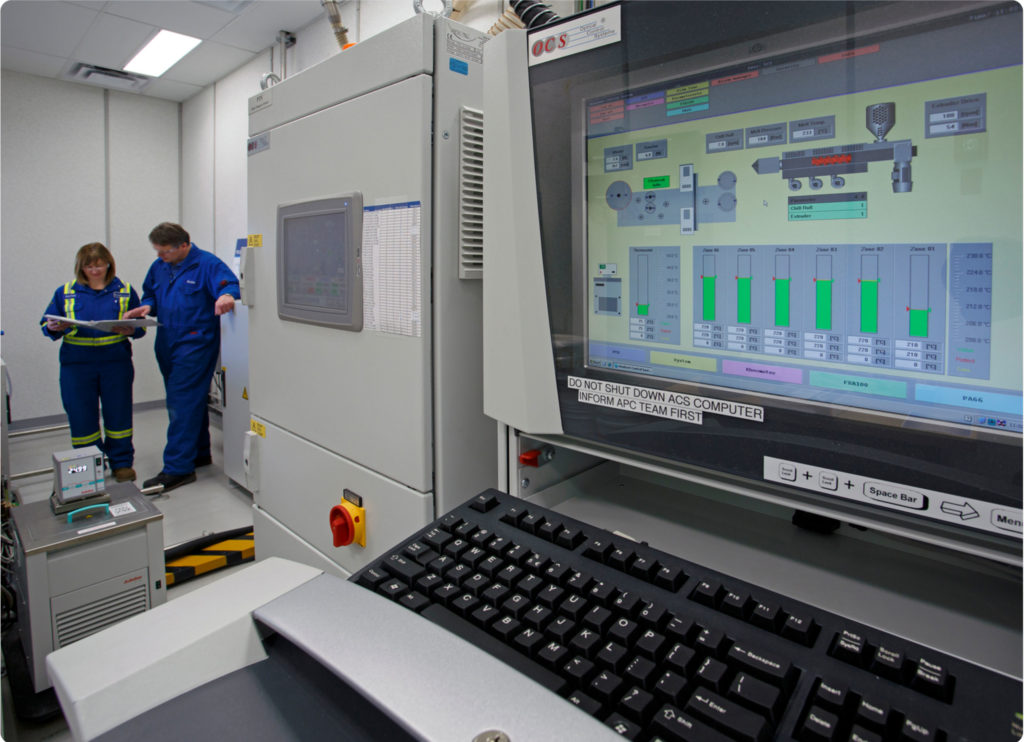
Quality Assurance
At-line data enables us to identify infrequent or short-lived quality excursions and gain a better understanding of the consistency of individual batches. As a result, we have a greater ability to consistently ship lots that meet our customers’ expectations.
Metal Detection
We understand the issues metal contamination can cause in metal-sensitive markets such as caps and closures and food packaging. To mitigate these risks to customer equipment damage, product failures and even consumer health, we’re making continuous investments in advanced metal detection and separation technology.
Streamer and Fines Mitigation
Streamers and fines can cause resin transferring challenges at our customers’ facilities. To minimize the quantity, each of our plants has systems such as screens, elutriators and scalperators that remove them from the product. We also have ongoing initiatives to upgrade our systems’ design to optimize resin transfer conditions. The goal of this work is that our customers receive the most defect-free possible products.
Railcar Security Enhancements
Serial numbers on cable seals must match shipment documentation in order to verify that the resin was not tampered with during railcar storage and transportation. We recently completed a project to eliminate the manual data entry steps needed to capture these seal numbers. Now, this process is fully automated via mobile devices, cable seal bar codes and railcar RFID tags, ensuring customers that their product has remained untouched en route.