Centre for Performance Applications
Dedicated to polyethylene applications development work for rigid and flexible markets.
Bring your ideas to life without interrupting your production line
Located in Calgary, Alberta, the Centre features state-of-the art extrusion, conversion, molding and test equipment that replicates customers’ manufacturing methods and application performance under real-world conditions. Expert engineers, scientists, and technologists perform the critical work to improve today’s applications and even reimagine how PE resins are used.
Flexible Film Applications
Rigid Applications
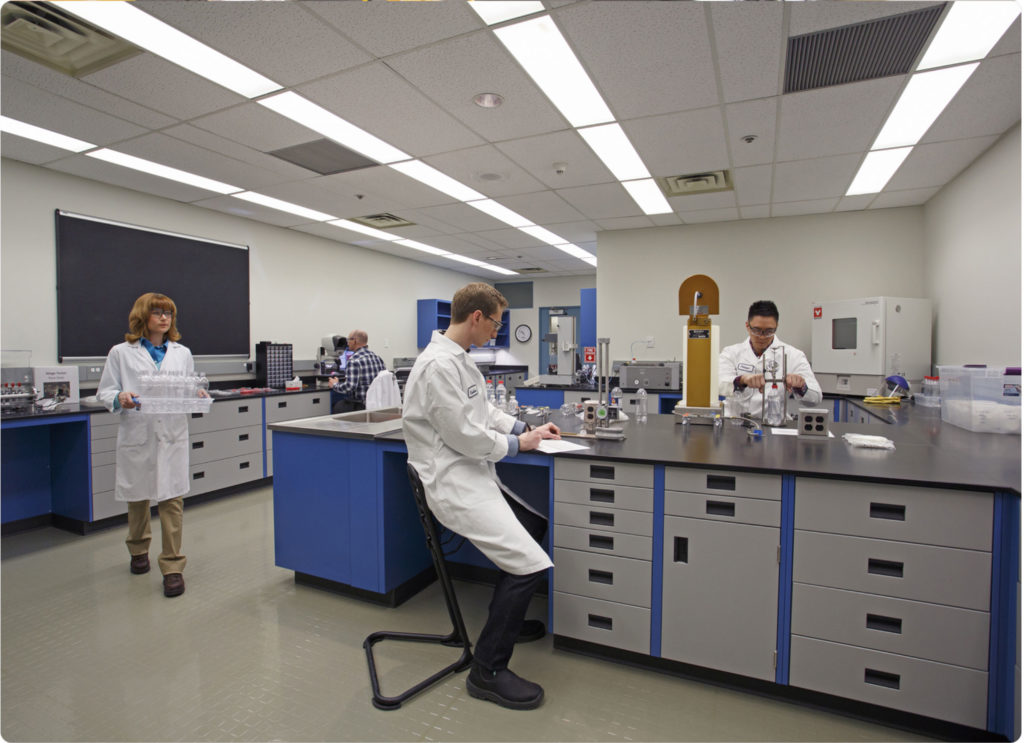
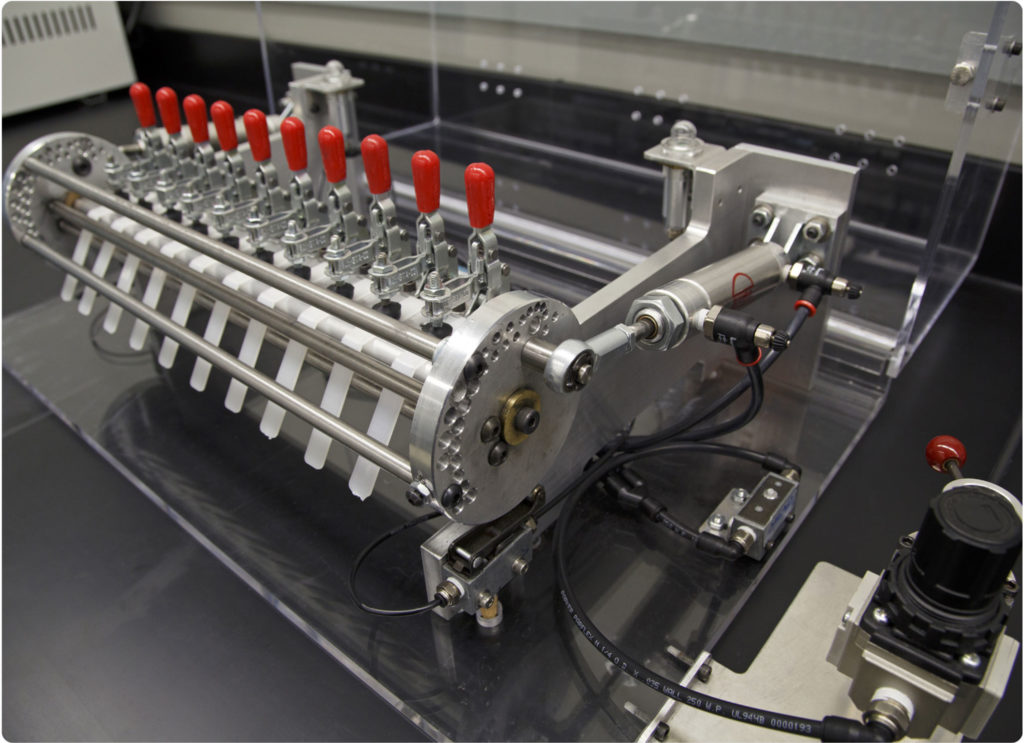
Caps and Closures
A SACMI compression molder and Sumitomo Demag injection molding press replicate caps and closures’ manufacturing processes, while our state-of-the-art dedicated closures lab features an advanced a suite of industry-leading “in-use performance” equipment to measure performance under real-world conditions. We follow the International Society of Beverage Technologist (ISBT) standard testing methods and have proprietary testing methods and equipment as well. Exclusive simulation capabilities and advanced material models streamline the qualification process for new closures or resins.
Proprietary Caps & Closures Living Hinge Tester
When we identify the need for entirely new test equipment, we’re known to create it ourselves. Such was the case with a hinge tester for polyethylene closures. Eliminating the need for manual input, our hinge tester can run continuously to test cap fatigue performance, allowing us to gauge how well the hinge will perform in the consumer’s home.
Rotomolding
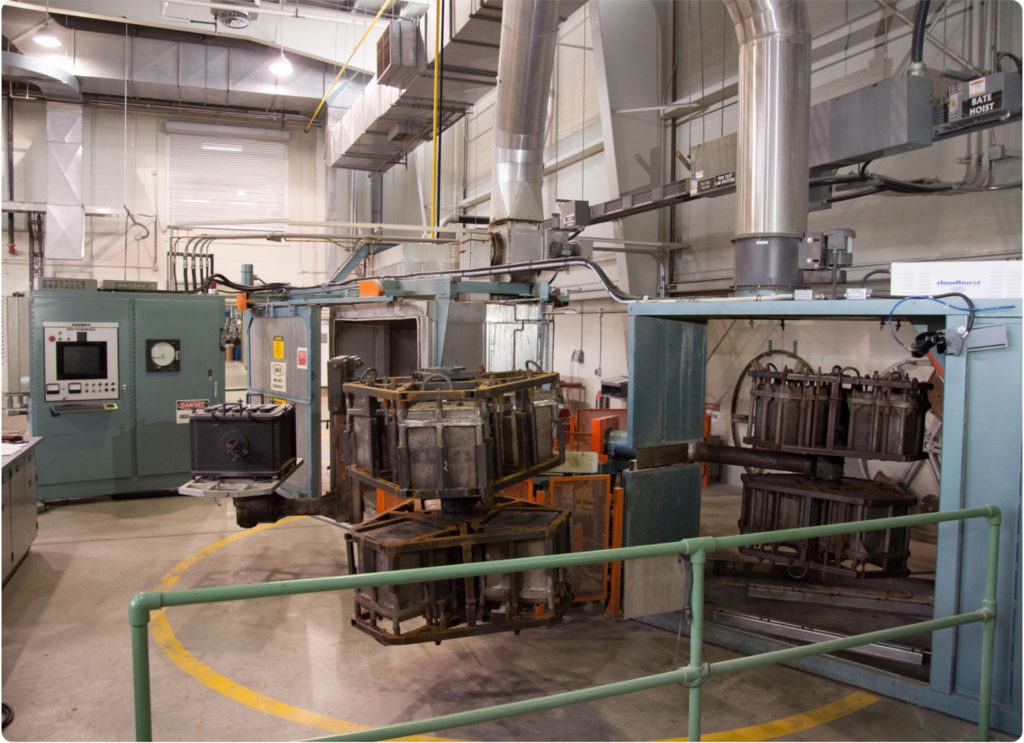
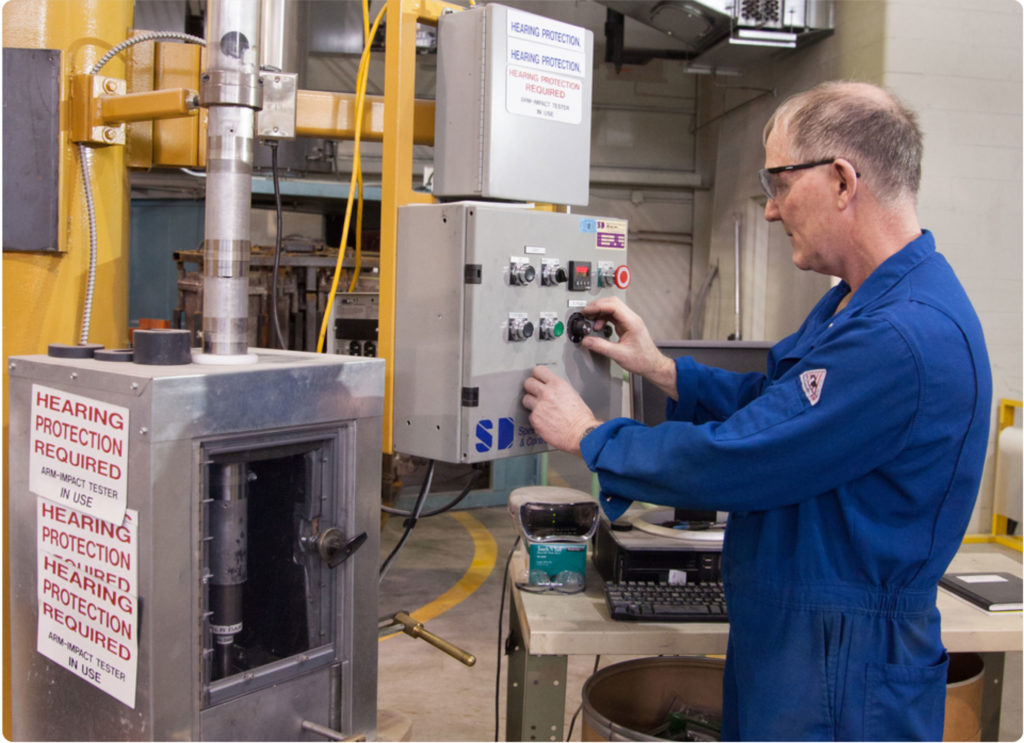
The applications work we do for the rotomolding market helps our customers understand how to improve part reliability and quality, process control, and cycle times. Some of the experimentation, testing and assessment that takes place at the Centre is for the Association of Rotational Molding for the holistic advancement of the industry. Our work is supported by a range of equipment including:
- Ferry rotational molder, a three-arm independent carousel machine, featuring upgrades for infrared temperature sensing and a drop-box for two-layer and mixed material parts
- A variety of testing instruments, including high-speed impact data acquisition and additives analysis
- ORENDA Airforce grinder for commercial quality grinding of small batches
The Starting Point for Innovation
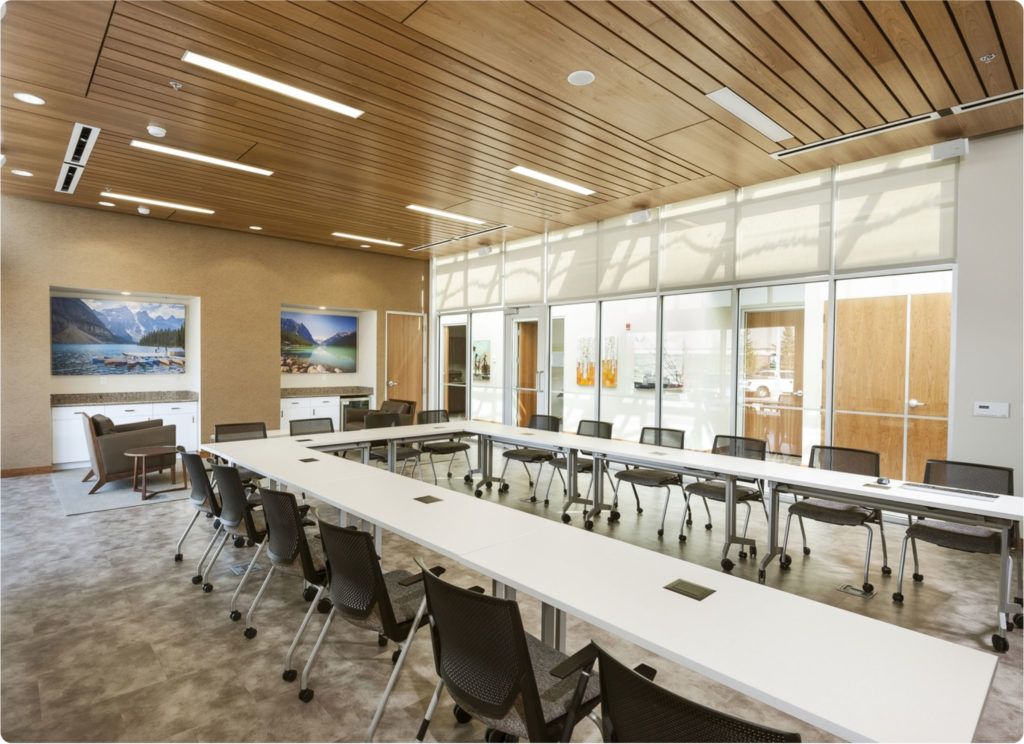
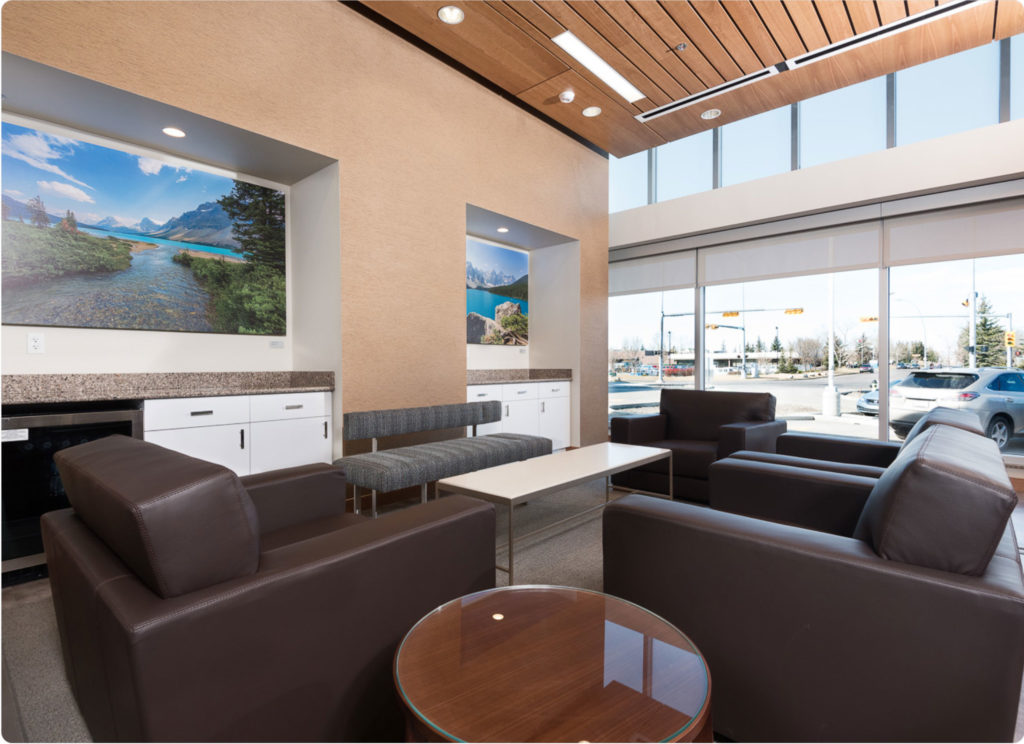
Come work with us! Our Centre for Performance Applications serves as an innovation hub where customers can work with NOVA Chemicals’ experts to generate new ideas and applications. Expansive areas are dedicated to collaborative work including ideation sessions, workshops, and trial evaluations.